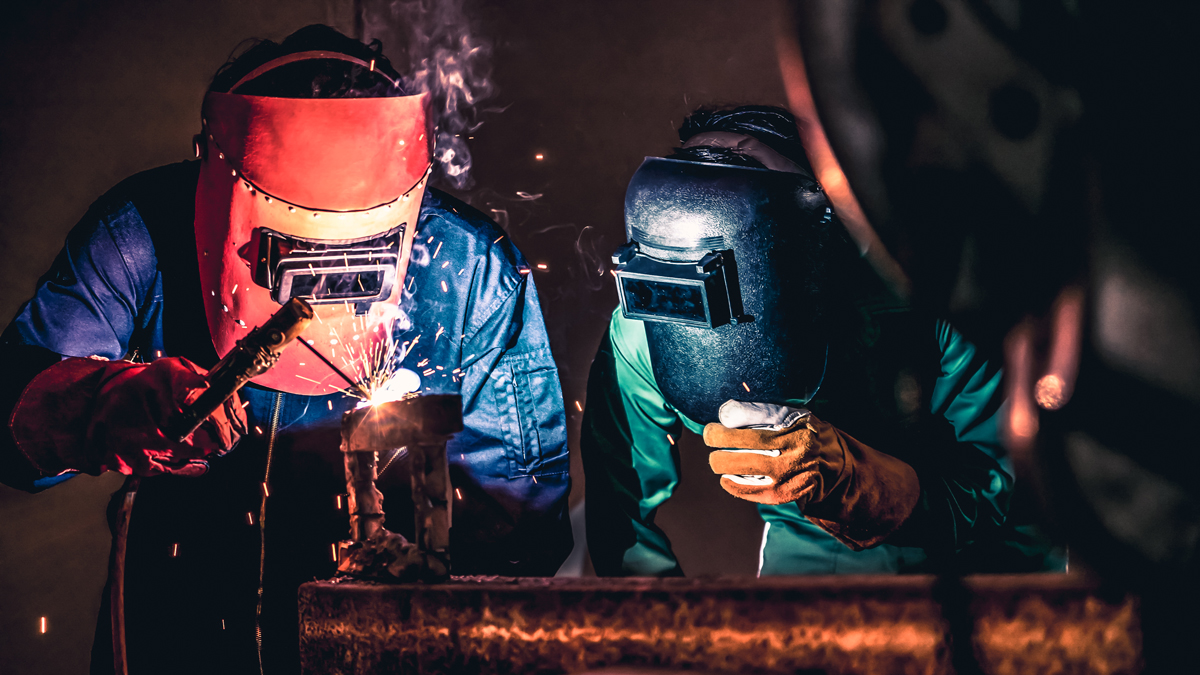
Choosing the correct welding process for your needs will make or break your work. Unfortunately, there is no universal welding process. This is due to the fact that different metals and materials exist, each one with their own unique properties that have to be accounted for.
Welders, especially beginners, are often wondering which welding process should they use. It is always good to know all of them, or at least learn the basics of each one of them. This will make you an all-around welder that can weld almost any type of material.
But you still have to decide how to approach a certain project when it comes to the welding technique you have to utilize.
What to Consider When Choosing the Right Welding Process
Whenever you need to weld, you can’t simply start doing it right off the bat. There are a few things that you have to consider which will ultimately help you in picking the correct technique. First, think about the materials that you are going to be working on. All of them are different and the wrong one may result in a weak weld or will utterly destroy your work.
You also have to consider the quality and the appearance of the weld that you are striving towards. You don’t want to end up with a nasty looking weld on a piece of furniture that is supposed to look beautiful.
Most welders will agree that there are four areas that you have to consider when choosing the right welding technique – fill amount, speed of travel, position, and penetration.
What Process Meets Those Requirements
After you know what you want out of your weld and have an idea how everything should look, time to choose. There are four types of welding techniques that are most used – MIG, TIG, Stick, and Flux.
Each one of them has its own unique characteristics that are supposed to help you achieve what you need.
MIG Welding
MIG welding is a gas metal arc welding process that is considered as the easiest one to learn. With it, welders have good control when welding which is particularly useful with thinner materials.
If you use Pulse MIG welding, an extension of MIG, you can end up with high quality welds on materials of various thicknesses. You can work on steel, stainless steel, aluminum, and even superalloy.
MIG welding is a process that creates clean welds with less slag.
TIG Welding
TIG Welding is also a gas metal arc welding process with the main difference being that it is using a tungsten electrode. TIG is also a versatile process that can be used to weld metals like stainless steel, magnesium, aluminum, copper, titanium, and brass.
TIG is a bit harder to learn and requires more practice and training to master. But when achieving it, welders can create high quality welds that are aesthetically pleasing. Also, keep in mind that there are AC and DC types of TIG welding. Most high-quality TIG machines are the AC TIG type. Only AC TIG welders can weld aluminum while DC TIG machines can weld regular steel. However, around 85% of welding is conducted using AC. You can read more about AC welding here.
Stick Welding
Stick welding is the oldest process and has been used by welders for years now. It is also known as shielded metal arc welding and uses an eclectic current flow that is created from a gap between the metal and the arc-welding electrode.
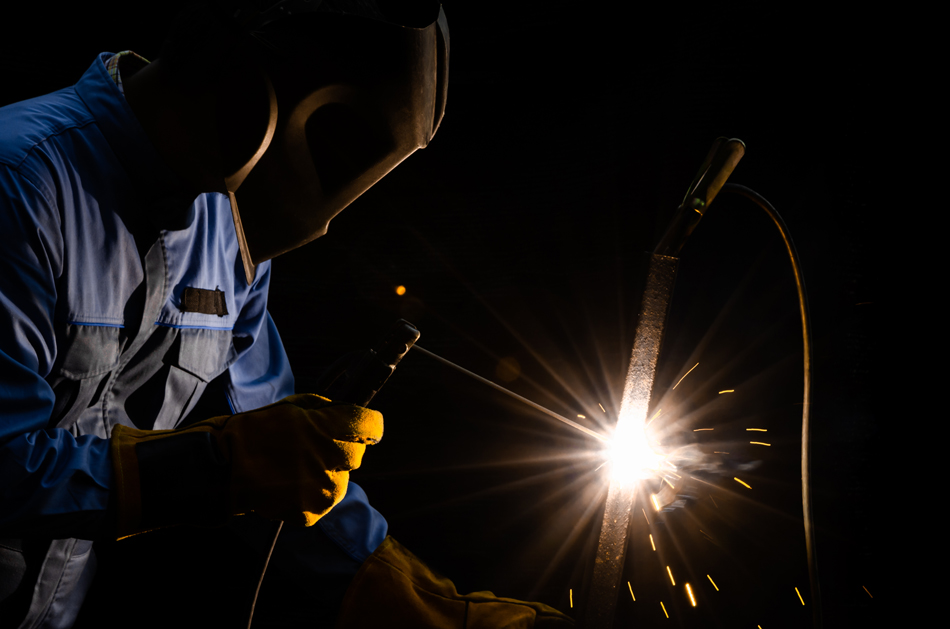
With stick, you can weld both outdoors and indoors. It is especially useful when working in windy conditions. More so, it can cover all the basic joint welds that you need to do around the house. It is the most economical technique out of them all and can also work well on rusty and dirty materials.
However, stick welding is not very clean, it is difficult to maser and it is difficult to weld thin metals with it.
Flux Core Welding
The Flux Core welding process is perfect for achieving deeper penetration on thicker materials. This is a wire-feed process but is self-shielded and does not require the use of a shielding gas. The flux-core wire itself is the one that shields the arc from contamination.
While this process works best on mild materials, like stainless steel, it’s far less forgiving when working on dirty or rusty materials than other processes are. It has the ability to increase metal deposition rate and is good for out-of-position welding.