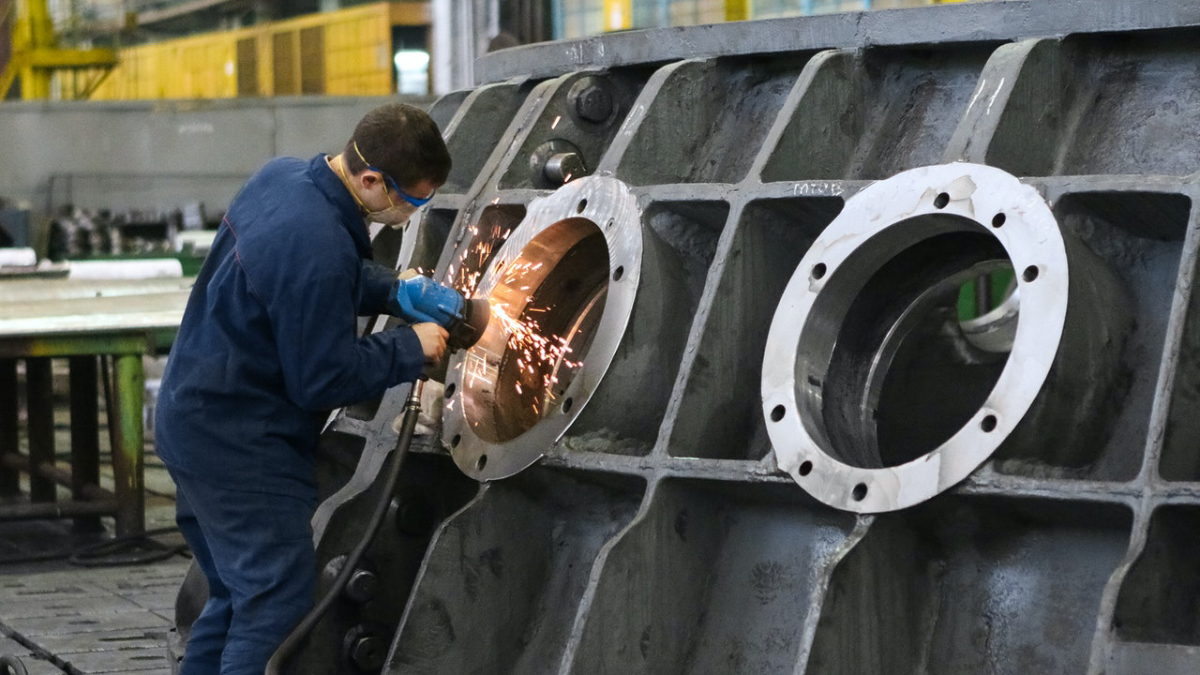
From being used in food production, pharmaceutical, chemical processing, and even in the automotive industry, industrial ovens are dynamic. Basically, these ovens are heated chambers used for drying parts, baking, and curing various products at various stages of production.
They come in different sizes for different applications.
Some are in batches and others in conveyor lines. Their configurations are of different ranges. And if you needed to know more, we’ve researched and come up with some of the most common uses of these ovens.
Medical Equipment Sterilization
Sterilization plays a vital role in the health and pharmaceutical industries as well as research labs. Medical professions use industrial ovens for sterilizing their instruments and devices. Syringes, scalpels, surgical staples, and metal rods are all decontaminated using industrial ovens- and it is effective and reliable. These ovens are especially useful as they have the flexibility of controlling the temperature to get the ideal temperature of eliminating all the microbes, bacteria, and viruses that may be present in medical devices.
Heat Treatment
Most products involve the application of heat at a certain temperature to attain the desired result. In essence, they are involved in stress relief, annealing, tempering, and aging. These processes require set temperatures for ideal treatment to occur.
The procedure of lessening of the hardened metal brittles is tempering, and it requires controlled but stable conditions to balance between hardness and ductility. On the other hand, stress relief involves the application of heat to products so as to mitigate the effects of residual, structural, and other stresses. Stress results from cold working, shearing, or gas cutting.
When it comes to aging in the heat treatment of materials, stimulation of time effect is efficient with industrial ovens. For example, the aging of aluminum materials hardens them to enhance their ductility and durability. Experts at pqovens.com say that to avoid damage and cracks, the aging process requires a slow but steady temperature for a period of time – hours or days. The annealing process also serves to increase the ductility of materials by heat treatment.
Used in Pharmaceutical Industry
Industrial oven innovation transformed the pharmaceutical industry in a major way. This is because these ovens are efficient in baking the coating of pills. Also, thermal oxidizers used in these ovens help eliminate any excess chemicals that might be produced in the manufacture of pharmaceutical products.
Testing Materials
Industrial ovens revolutionized testing materials. They are used for burn-in testing of various materials. The type of industrial ovens that are used for this is made for the dynamic and static burn-in of electronic devices and integrated circuits.
For Drying Materials
In industrial operations, drying serves a range of purposes. In pharmaceutical industries, this may mean curing the pills. It may also refer to the decontamination of equipment. Industrial ovens also come in handy in tower drying as they are designed for packaging, coating, and printing.
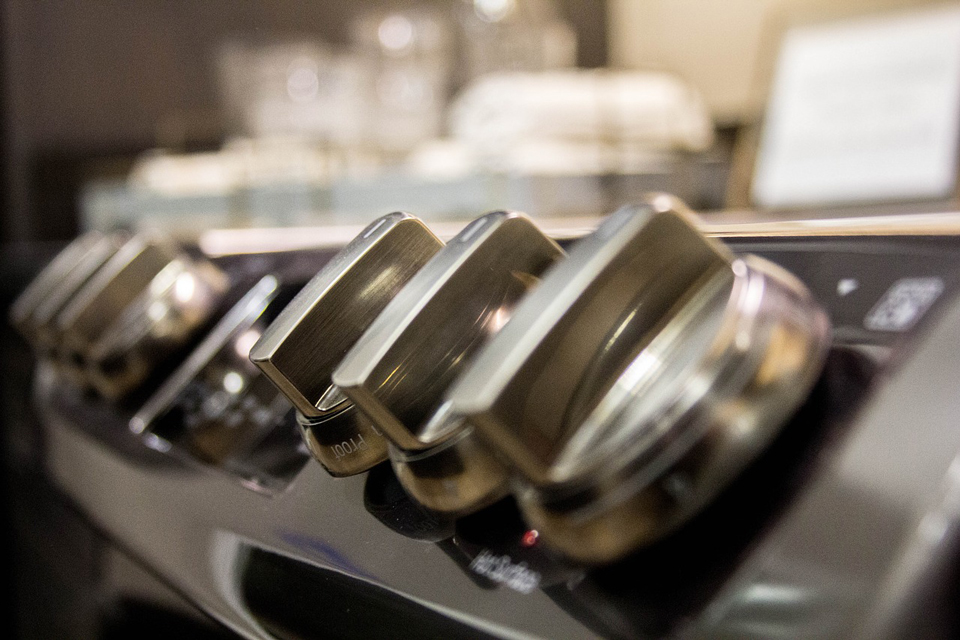
Sintering
Industrial ovens are used to bond and compact materials below the melting point. This is the sintering process. It is a process that enhances the density and strength of materials. Various industries, including the dental industry, metallurgy, and metal molding, use the sintering process to pre-heat, heat at extreme temperatures, and cool down materials to achieve the desired effect.
So, what are the common types of industrial ovens and their unique uses? All industrial ovens are not equal, and their specifications, type, and uses vary. Below are some ovens you should know about.
- Curing Ovens: they are used for heat treatment that accelerates chemical reactions in a process known as curing. They are especially useful in materials such as adhesives and rubber.
- Dying Industrial Ovens: Designed for eliminating moisture on products, these ovens are incredibly reliable. They undertake the treatment through a 3-stage process; heating, soaking, and cooling down the stage. In the heating stage, the temperature is set to remove all the moisture in a predetermined time. The materials are then left to soak in the heat for a period of time before being passed through heated and cooler air as the final stage.
- Batch Ovens: These are perhaps the most dynamic ovens capable of various heat processes, including drying, annealing, aging, and curing. And, depending on the production requirements, they have racks, carts, and trucks to place the raw materials.
- Continuous Industrial Ovens: they are especially great for mass production of products and maintain the same quality for every product. They are used for processes that use the same materials. What sets them apart from other industrial ovens is their separate heating and cooling chambers.
If you were looking to understand the uses of these dynamic ovens, this article highlights them for you. Industrial ovens are used in manufacturing, processing, and electronic companies more often than we imagine. From medicine to aeronautics, their applications are endless.