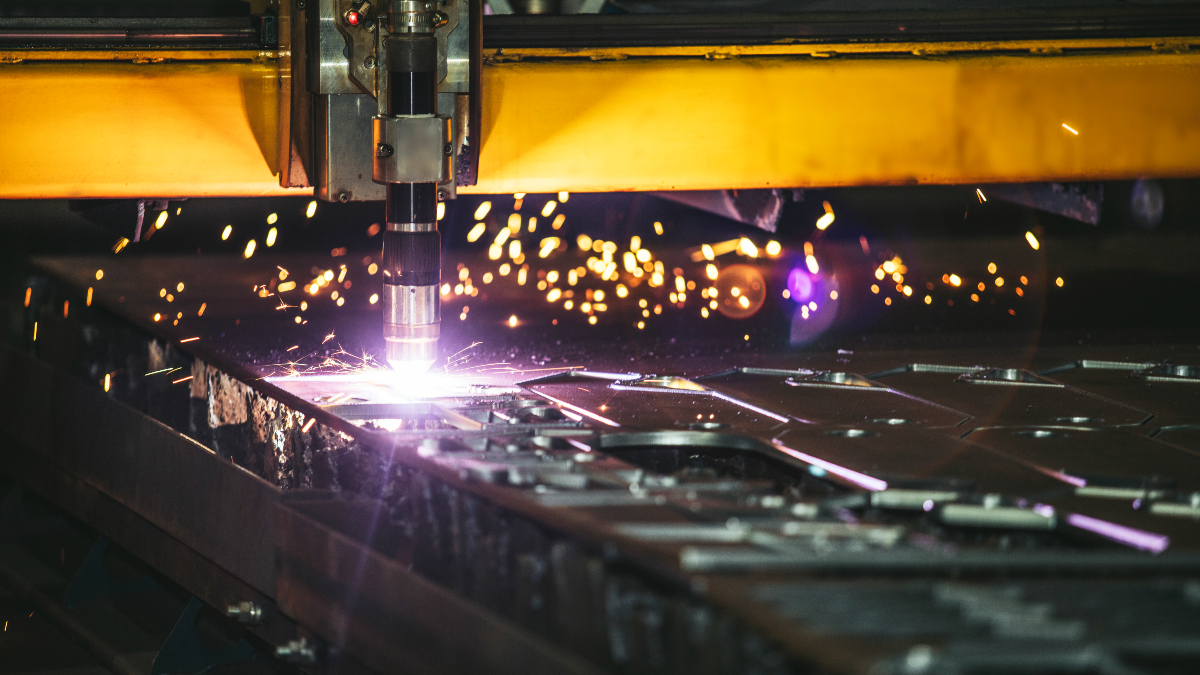
Once upon a time, humans did everything by hand, this includes the repetitive cutting tasks required to complete manufacturing projects. Just think about what it would look like if humans needed to cut each potato by hand, used in the creation of potato chips. Things would take a long time and, you can bet, that a $2 bag of chips is suddenly going to be much more expensive. That’s just one example of things that need to be cut and, ideally, need to be cut in a more efficient manner than by human hands.
Take a look around the room you’re in right now. What has been cut away from a larger piece? Almost everything right?
Luckily for modernity, there are solutions to our incessant need to cut things down to fit them within packages or make them the correct size for a consumer. Of course, on a large scale, these solutions are often used by businesses not home consumers; they’re designed to help people mass-producing items that need to be cut, more so than personal use in the back of your garage.
The following will explore the world of industrial cutting systems which have been central to the manufacturing industry since the industry first began to pick up steam. It’s important to note that we’re talking about a huge range of processes here. It can include sawing, milling, hewing, drilling, turning, shearing, scissoring, grinding, policing, flame-cutting, plasma cutting, laser cutting, and etching just to name a few of the options.
It’s also essential to note that many of these processes require management and oversight by experienced professionals, as machinery on this scale can be dangerous if proper safety precautions are not followed. Always be sure to understand the safety protocols before operating any piece of heavy equipment, and stop and ask for clarification if you have any doubts at all about the system you’re working with.
The Basics: What Is Cutting?
Because the idea is so simple, it’s one of those terms that people might wonder if it has a different meaning in manufacturing than in everyday usage. When it comes to manufacturing, cutting does basically mean the same thing as it does when you’re talking about cutting a label off the new sweater you bought. It is the process of creating something by removing unwanted material from a larger piece of material.
Different Products Require Different Industrial Cutting Systems
Depending on what you’re cutting, you might need an entirely different system than another product’s manufacturing team might need. Even products that at first seem similar might require different cutting systems.
Think about the potato chip example from above. Chips are potatoes cut very thin. French fries are also cut potatoes. So are crinkle-cut fries and curly fries. Think about hash brown cubes. While all these products are cut potatoes, they require different cuts and therefore, different systems.
Heat Cutting
When it comes to cutting materials that are tough, one of the more common approaches involves using heat to help make the necessary cuts. Because of this, heat cutting has become a major part of the manufacturing process. Heat cutting can include flame cutting, plasma cutting, and laser cutting.
Flame Cutting
Flame cutting involves using fire to cut through a material, often a thicker metal. The process involves a lot of the same technological groundwork as welding as the temperature of the flame used can make the difference between a successful cut or an unsuccessful one. A flame cut essentially burns a line through the object being cut.
The most common tactic is called oxy-fuel cutting. This involves using a torch to raise the temperature of a metal to its kindling temperature. Once this is done, a stream of oxygen is directed at the metal. This burns it into a metal oxide that flows away in the form of molten metal, sometimes called dross.
If someone is working around flame cutting they need proper eye protection as the brightness of staring into the fire can damage the eyes, as can flying sparks. Moreover, proper ventilation is needed, and air pressure must be monitored to ensure it stays within safe ranges for this type of work.
Plasma Cutting
Plasma cutting is often used to cut through materials that are conducive to electricity using a jet of hot plasma. Steel, stainless steel, aluminum, brass, and copper are all examples of materials that are typically cut using a plasma cutter, though other metals that are conductive can be cut too. You might find this type of cutting in fabrication shops, auto repair and restoration, industrial construction, salvaging, and scrapping.
Plasma cutting tends to be one of the less expensive options for cutting strong materials. It’s also something that tends to be done with great speed and precision. Because of this, plasma cutting is becoming more popular in smaller businesses and hobbyist shops.
Again, proper eye protection is needed, as are face shields. This will protect the eye from being damaged by the brightness or by debris. Leather gloves and protective clothing are also recommended. You also need a safe surface with which to work; there are plasma tables for sale if you know where to look. Further, you need to work in areas that are free of flammable materials (sparks can cause fires).
Laser Cutting
Laser cutting is another industrial cutting technology. It uses a high-power laser to vaporize materials resulting in a cut. This option allows for intense precision and dimensionally accurate cuts, etching, drilling, or engraving.
Like the other methods, safety glasses are needed to protect the eyes from particles and debris while operating. Proper ventilation is essential as laser cutters can generate fumes. Skin protection is also needed to reduce the risk of burns. Moreover, laser cutting can get loud, so hearing protection is also recommended.
The above information should give you an introduction to heat-based industrial cutting systems. It is crucial that you do not cut material with any of these systems unless the manufacturer has approved that material for cutting with their system.